Elon Musk: The Challenges of Mass Electric Vehicle Production 🚗⚡️
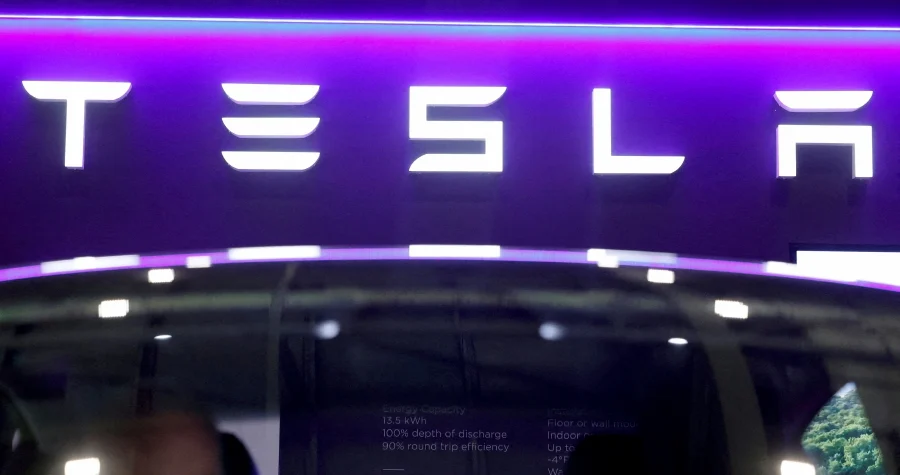
Elon Musk: The Challenges of Mass Electric Vehicle Production 🚗⚡️
Elon Musk—a name etched into the annals of technology and automotive history—has crafted an inspiring tale of innovation, ambition, and unrelenting vision. As the driving force behind Tesla, Musk has propelled electric vehicles (EVs) from a niche curiosity to a global phenomenon, reshaping how the world views transportation. Yet, this journey to conquer the EV market has been anything but smooth. Beneath the triumphs lie a series of formidable challenges—production bottlenecks, technical hurdles, and financial gambles—that have tested Musk’s resolve and Tesla’s endurance. This article dives deep into the thorns that have pricked Tesla’s path under Musk’s leadership, exploring the obstacles faced in mass-producing electric vehicles and the lessons that have emerged from this electrifying saga.
A Difficult Beginning
Tesla’s early foray into mass production was less a victory lap and more a fight for survival. Founded in 2003 by Martin Eberhard and Marc Tarpenning, Tesla welcomed Musk as chairman and major investor in 2004, with a vision to make EVs mainstream. The Model S, unveiled in 2012 as Tesla’s first mass-produced car, was a bold step toward that dream—a sleek, all-electric sedan promising luxury and sustainability. But behind its glossy exterior lay a production process riddled with growing pains.
Quality issues plagued the Model S rollout. Early customers reported faulty door handles, misaligned panels, and software glitches—blemishes on a car meant to rival the likes of BMW and Mercedes. Securing a stable supply chain proved even thornier. Batteries, the lifeblood of any EV, were in short supply, with Tesla relying heavily on Panasonic for lithium-ion cells. Delays in component deliveries stalled assembly lines, while manufacturing hiccups—like inconsistent paint finishes—drew scrutiny. Musk, then CEO, threw himself into the fray, often sleeping at Tesla’s Fremont factory to oversee fixes firsthand. “I was living in the factory for months,” he later recalled in a 2013 interview, a testament to the hands-on grit that defined those early days.
The stakes were high. Tesla was burning through cash—$4.6 billion in losses by 2012—and teetering on the edge of bankruptcy. Musk’s personal fortune, bolstered by his PayPal windfall, kept the company afloat, but the Model S had to succeed to prove EVs could scale. By 2014, Tesla ironed out many kinks, delivering 31,655 Model S units worldwide, but the rocky start underscored a harsh truth: mass production was a beast far tougher to tame than Musk had anticipated.
“Production Hell”
The phrase “Production Hell” entered Tesla’s lexicon with the Model 3, a car meant to bring EVs to the masses. Unveiled in 2016 with a $35,000 price tag, the Model 3 garnered over 400,000 pre-orders in weeks—a tidal wave of demand that Musk vowed to meet with a target of 5,000 cars per week by 2018. That goal became an obsession, but the road to it was a descent into chaos.
Fremont’s production lines buckled under the strain. Conveyor belts jammed, parts piled up, and bottlenecks slowed output to a crawl. Musk’s push for automation backfired—robots struggled with tasks like installing seats or aligning panels, tasks humans could do faster. Workers clocked grueling shifts, some reportedly sleeping in the factory alongside Musk, who dubbed it “the hardest thing I’ve ever done” in a 2018 New York Times interview. The pressure was palpable; Tesla missed its 5,000-weekly mark by months, hitting it only in June 2018 after erecting a temporary “tent” factory to boost capacity.
Musk later admitted he’d underestimated the leap from boutique production (Model S and X) to mass-market scale. “We were naive,” he said on a 2018 earnings call, reflecting on how Model 3’s complexity—simpler than the S, yet still packed with tech—overwhelmed Tesla’s systems. The ordeal cost billions and nearly sank the company, but it also forged a resilience that would define Tesla’s future. By 2025, Model 3 production hums at over 1 million units annually, a phoenix risen from the ashes of “Production Hell.”
Battery Issues
Batteries are the beating heart of electric vehicles, and for Tesla, they’ve been both a lifeline and a chokehold. Producing efficient, safe, and affordable battery packs has been a persistent challenge, one Musk has tackled with a mix of partnerships and in-house innovation. Early on, Tesla leaned on Panasonic, co-developing cells at the Gigafactory in Nevada, opened in 2016. But supply couldn’t always keep pace with demand—shortages in 2017 delayed Model 3 deliveries, forcing Tesla to scramble.
Quality control was another hurdle. Lithium-ion batteries must balance energy density, longevity, and safety—overheating risks, like those in rare Tesla fires, demanded rigorous testing. Musk pushed for breakthroughs, unveiling Tesla’s 4680 battery cells in 2020—larger, more powerful, and cheaper to produce. By March 2025, these cells power the Model Y, boosting range to 400 miles, but scaling production has been slow. “Battery ramp-up is exponential,” Musk tweeted (@elonmusk, March 10, 2025), acknowledging the painstaking process of perfecting yields.
Tesla’s vertical integration—building its own cells while still collaborating with CATL and LG Chem—has eased some pressure, but the battery bottleneck remains a tightrope walk. Musk’s obsession with energy density and cost reduction is key to Tesla’s edge, yet it’s a reminder that even a visionary can’t fully tame the chemistry of mass production.
Automation and Humans
Musk’s love affair with automation is well-documented—he’s called Tesla factories “the machine that builds the machine.” His vision was a fully robotic assembly line, slashing labor costs and boosting efficiency. But reality bit hard during Model 3’s rollout. Robots, programmed for precision, faltered on variable tasks—think threading wires or fitting soft interiors—leading to delays and defects. Maintaining and repairing these machines ate up time and money, with Tesla spending $1.3 billion on capex in 2017 alone.
The over-reliance stung. In a 2018 CBS interview, Musk conceded, “Excessive automation was a mistake… Humans are underrated.” Tesla pivoted, hiring more workers—Fremont’s staff swelled to 10,000—and rebalancing the human-robot dynamic. By 2025, Gigafactory Shanghai exemplifies this hybrid approach: robots handle repetitive welds, while humans finesse final assemblies, churning out 2,000 cars daily. Musk’s lesson? Automation is powerful, but flexibility demands a human touch—a pivot that’s optimized Tesla’s output without sacrificing quality.
Production Costs
Tesla’s mission hinges on affordability—making EVs accessible beyond the luxury crowd. The Model 3’s $35,000 sticker was a bold promise, but early costs soared past projections, with production inefficiencies and premium features driving prices up. Musk attacked this from all angles: streamlining designs (fewer parts per car), securing cheaper suppliers (like China’s CATL for batteries), and scaling Gigafactories—Nevada, Shanghai, Berlin, and Texas—to cut shipping and labor overheads.
By 2025, Tesla’s average cost per vehicle has dropped to $36,000 (Bloomberg), down from $50,000 in 2018, but balancing cost and quality remains a tightrope. Cheaper batteries risk range cuts; simpler designs can alienate buyers expecting Tesla’s tech edge. Musk’s answer is relentless optimization—tweaking everything from paint processes to seat stitching—while betting on economies of scale. The Model Y, now outselling gas SUVs in Europe, shows progress, but affordability is still a moving target in a competitive EV market.
Overcoming Difficulties
Despite the gauntlet of challenges, Tesla has thrived where others might’ve folded. Musk’s persistence—sleeping in factories, pouring in personal funds—kept the dream alive during 2008’s financial brink and 2018’s production abyss. Innovation fueled recovery: the Gigafactory network, now producing 2 million cars yearly, solved supply woes; 4680 cells cut costs; human-robot synergy streamlined lines. Creative problem-solving—like the Shanghai tent or Tesla’s “Megapack” energy sideline—turned crises into opportunities.
The Model 3, once a production nightmare, is now the world’s best-selling EV, with over 2 million units sold by 2025. Tesla’s global footprint—plants in four continents—cements its dominance, delivering 1.8 million vehicles in 2024 alone (Tesla Q4 Report). Musk’s ability to pivot, endure, and innovate has turned thorns into triumphs, proving that sheer will can bend even the toughest challenges to submission.
Lessons Learned
Tesla’s saga offers a playbook for EV makers worldwide. Mass production demands more than cutting-edge tech—it requires a slick supply chain, a tireless workforce, and a management strategy that adapts on the fly. Musk’s early missteps—over-automation, supply neglect—teach humility; his recoveries—Gigafactories, human integration—teach resilience. Competitors like Rivian and Lucid, scaling their own EVs, can glean this: success isn’t just engineering; it’s execution. Musk’s bold vision, paired with a willingness to grind, shows that the impossible bows to those who refuse to quit.
Conclusion
Tesla’s journey to mass-produce electric vehicles is a testament to perseverance, ingenuity, and the power of dreaming big. From the Model S’s shaky debut to the Model 3’s hellish ramp-up, Musk has faced hurdles that would’ve crushed lesser spirits—supply crises, automation flops, cost overruns. Yet, through it all, Tesla has laid a foundation for an electrified automotive future, with over 5 million EVs on roads by 2025 (Statista). Challenges remain—battery scale, market rivals—but Musk’s leadership proves that audacity and grit can turn thorns into milestones. Elon Musk has shown the world that big dreams become reality when you dare to think, dare to act, and never, ever give up. 🚀